How have welders influenced welding helmet design?
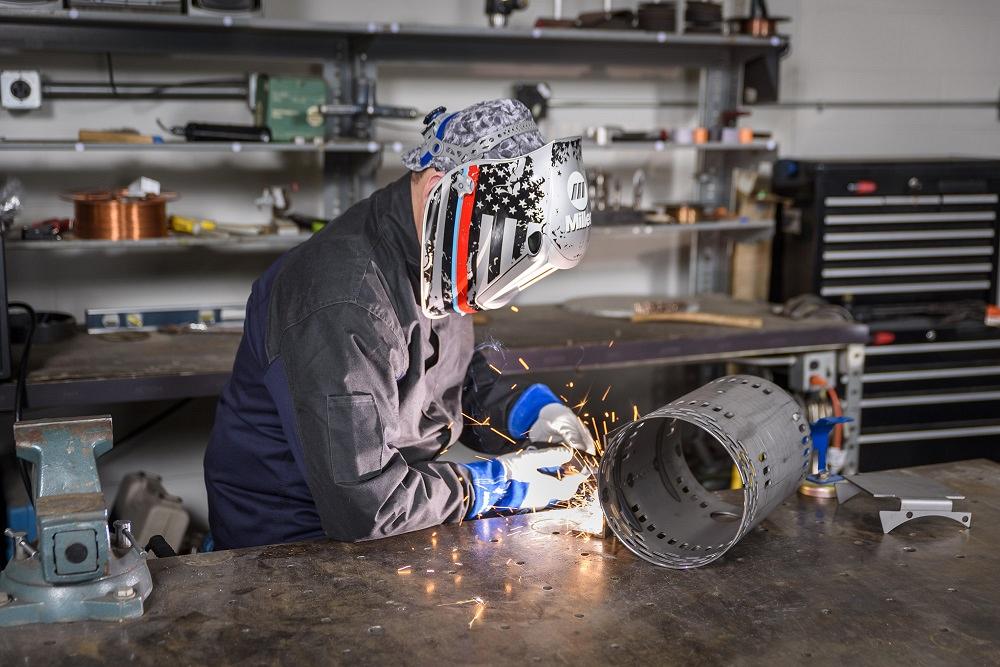
Welders past and present have helped pave the way for how welding helmets look and feel and what features they provide. This can be seen in the higher-end models, middle-of-the-line options, and the basic helmets. Miller Electric Mfg. LLC
Take a quick glance at today’s welding helmets and you may wonder how to use and master all the features.
Nowadays, you can find autodarkening, natural color, lightweight, and ergonomic features on higher-end welding helmets, middle-of-the-line options, and the more basic models (no, manufacturers haven’t forgotten about those customers, either). Some welding equipment manufacturers argue that welding helmet advancements are the result of years of welder input—what they need from their helmet to make welding safer, more comfortable, more productive, and more efficient.
As long as welders continue seeking ways to improve their performance and work environment, manufacturers will continue to make improvements to their welding helmet offerings.
Seeing Under the Hood
In the early 1980s, Swedish manufacturer Hornell International—now part of Minnesota-based 3M—introduced autodarkening filters (ADFs) to welding helmets via its Speedglas line. This development revolutionized the industry because it allowed welders to see their work while keeping their eyes and face safe, all thanks to sensors that detected the instant the arc started or stopped.
Since then, multiple generations of ADF helmets have hit the market. 3M Technical Service Engineer Michael Hallock said a recent development in autodarkening technology is how some filters now curve to provide a closer fit to the user’s face for an improved field of view. Many times, the helmet may curve but the filter inside remains flat.
Hallock said TIG welders in particular asked for a better field of view from side to side.
“We curve it around your head because we don’t want to make a flat panel bigger because of weight, and because when you’re in a welding helmet and light comes in behind you, it’ll actually bounce off your helmet and [you] won’t be able to see as well.”
Hallock said helmet technology has advanced to the point where it allows the welder to see more natural colors while under the hood. Some helmets even provide variable color functions.
“Imagine I could take that natural color and I could shift it to cooler tones—bluer, let’s say—or I could shift it to redder, warmer tones,” he said. “Why would I do that? If I'm welding different materials or if I have different lighting, it can help me see the puddle better, it can help me see the joint better, and it can help me see the arc better based on the material I'm using and based on my personal preferences.
“The variable-color autodarkening filter—that is very interesting when I show it to people,” he added.
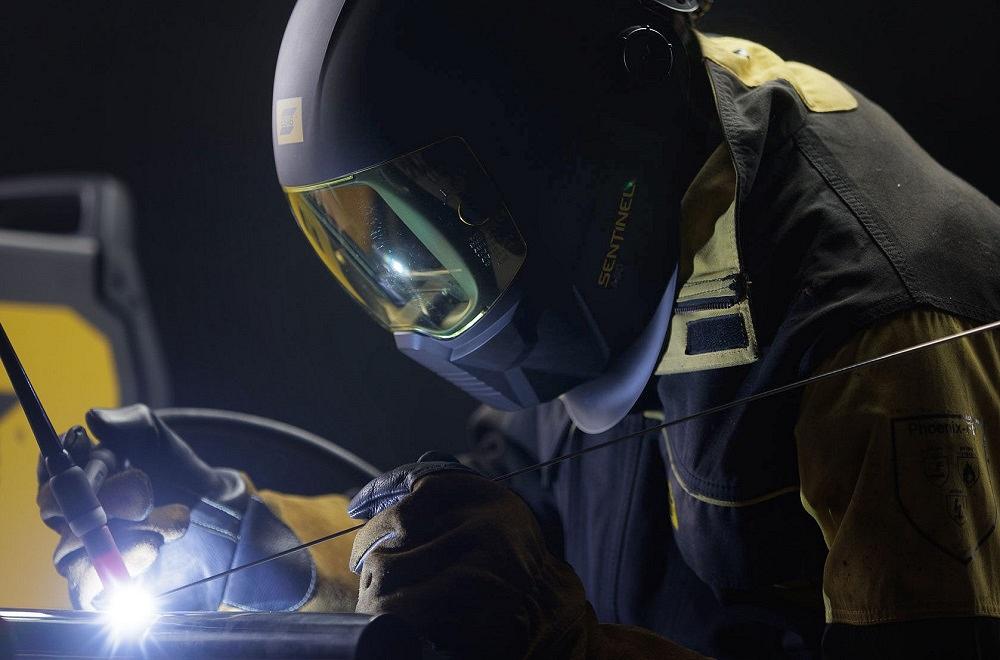
Some welding equipment manufacturers argue that the advancements made to welding helmets are the product of decades of welder input—all resulting in equipment that has made welding safer, more comfortable, more productive, and more efficient. ESAB
Welder Comfort
Welding helmet improvements go beyond what you can and cannot see while under the hood. As Kevin Beckerdite, global product manager of personal protective equipment at ESAB, put it, the attention “starts with the eyes, but it extends to the rest of the body.”
For instance, manufacturers take the weight of this equipment into consideration. If a welder is uncomfortable wearing a helmet while working, how will that discomfort affect their ability to weld?
In the early days, helmets were a rigid shape, thick and heavy. Today, a shift to thermoplastics has provided excellent impact protection that withstands abuse while still being thin and flexible.
“We want the whole welding helmet to be not only protective to your eyes, but to be like one with your body almost. The phrase I like to say [about welding helmets]: Make it so that it almost disappears,” Beckerdite said.
Advancements in welding helmet material and power supply sources have made this PPE as efficient and lightweight as possible. Beckerdite said ESAB has been able to increase the size of the ADF by 40% while weight changed by only 10 g.
But it’s not just about how much it weighs—it's also about how the weight is centered. Manufacturers have spent time ensuring helmets are properly balanced to help reduce head and neck fatigue.
“If you're not comfortable with what you're wearing, you're not going to want to do the job, or you're not going to want to do it safely,” Beckerdite said. “The goal is to make sure that everybody is doing the highest-performance job they can, as safely as they can.”
Something for Everyone
Manufacturers must be strategic when adding features to welding helmets, said Katie Kleman, product manager for Miller Electric Mfg. LLC.
While some metalworkers welcome the latest technology, improvements risk alienating those who are fine with their equipment or don’t need every feature.
Kleman described Miller’s line of welding helmets as a tiered lineup; each series provides the protection and comfort a welder needs to do any job, but features will vary. For example, an entry-level helmet may include a fixed-shade lens but not an ADF.
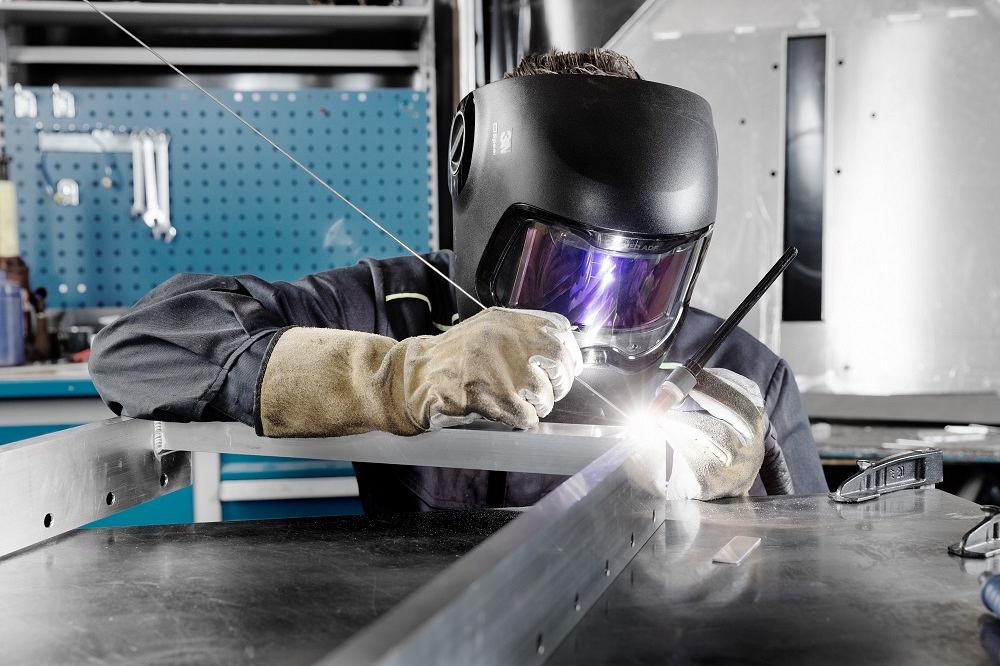
Equipment manufacturers predict that future welding helmet advancements will include more fine-tuning of current technology, more device connectivity, and more helmets with multiple PPE components. Much like past and present advancements, welders will help dictate what is and isn’t part of this equipment. 3M
A welding student at a technical school may not need the most advanced helmet, and a DIY welder may not need the same helmet features as someone in heavy industry, she added. Offering a variety of feature sets throughout the helmet series is important to appeal to different types of users, Kleman said. It gives welders the ability to tailor their equipment to their applications.
Nonetheless, Miller continuously adapts its equipment lineup and is pioneering the next steps in providing best visibility to help welders excel. For instance, a recent upgrade to its ClearLight lens technology provides a clearer and brighter view of the arc. Its HDV technology eliminates distortion when not welding head-on. And its X-Mode autodarkening feature assists welders who are working in settings where lighting is inconsistent.
Miller has also fielded customer requests for less urgent features, such as graphics and art on the helmets. Kleman said welders want to express themselves, not just through their work but also with what they wear.
“It's not a big tech thing, but giving people a chance to express themselves is great,” she said.
What Does the Future Hold?
Welders will continue to dictate how and where this equipment will develop.
Hallock said welders still have plenty on their wish lists and “holy grails” to attain in terms of improvements.
“As people strive to make things lighter, you have to make sure that it’s comfortable and can protect the welder in any applicable event that could happen,” he noted.
“When I talk to welders, what do they typically want?” Hallock asked. They want improvements to light technology, and they want “lights attached to so they can see better,” among other things.
Could augmented reality become part of future welding helmets? Hallock said he gets AR-related questions from customers.
Kleman expects manufacturers to continue fine-tuning technology that improves arc visibility and clarity.
“More and more employers are becoming safety-forward with providing welding helmets from high-quality manufacturers to improve welder retention, productivity, and safety, and Miller is excited to be a part of that,” she said.
Beckerdite said customers should expect higher-end helmets to become more affordable and accessible as welder well-being and welder efficiency converge. Making helmets with a powered air-purifying respirator (PAPR) and a grinding shield is the logical next step forward, but these features are complicated and expensive.
Some welders also wish to see helmets that include an attached hardhat and hearing protection.
“You wind up with layers of a helmet on top of your head, and a PAPR system attached to your back with the hose going up into your hood. You're adding a lot of protection but you're removing a lot of comfort along the way,” Beckerdite said.
“In many ways, it's like trying to balance the convenience with the protection and the cost. Solutions today are quite effective, but they’re pretty expensive.”
Solar panels, coin cell batteries, or a combination of the two typically power ADFs. They are lightweight and can last as long as 2,000 hours. Beckerdite said not to expect lithium-ion batteries to pop up on helmets, even as rechargeable power sources continue gaining relevance.
“It's kind of hard to justify adding the complexity and cost of [lithium-ion batteries],” he said. “In my view, at this point, rechargeable battery technology—while accelerating rapidly—is just not necessary for an ADF helmet right now.”
Twitter : https://x-i.me/weltut
Facebook : https://x-i.me/welfb
#Science Father#ResearcherAward #WeldingHelmetDesign #WelderFeedback #SafetyInWelding #WeldingInnovation #WelderComfort #WeldingVisibility
Comments
Post a Comment